Để nâng cao hiệu quả sản xuất của máy đóng gói hạt hoàn toàn tự động, chúng ta có thể bắt đầu từ nhiều góc độ, bao gồm tối ưu hóa thiết bị, cải tiến quy trình, đào tạo nhân sự và quản lý bảo trì. Dưới đây là một số phương pháp và gợi ý cụ thể:
1. Tối ưu hóa thiết bị
Chọn model máy phù hợp: Chọn model máy đóng gói phù hợp nhất dựa trên đặc điểm của sản phẩm (như kích thước hạt, mật độ, v.v.) và quy mô sản xuất. Đảm bảo các thông số hiệu suất của máy (như tốc độ, độ chính xác, phạm vi tải, v.v.) có thể đáp ứng nhu cầu thực tế.
Nâng cấp mức độ tự động hóa: Áp dụng công nghệ tự động hóa ở mức độ cao hơn, như hệ thống cho ăn tự động, cánh tay robot, v.v., để giảm sự can thiệp thủ công và cải thiện tính nhất quán và tốc độ vận hành.
Lắp đặt thiết bị đo lường hiệu quả: Sử dụng thiết bị đo thể tích hoặc cân có độ chính xác cao để đảm bảo lượng nguyên liệu được đổ đầy mỗi lần là chính xác và tránh phải làm lại hoặc lãng phí do sai lệch khi đổ đầy.
Hệ thống điều khiển được tối ưu hóa: Sử dụng công nghệ PLC và HMI (giao diện người máy) tiên tiến để đạt được khả năng kiểm soát chính xác và giám sát thời gian thực của quy trình đóng gói. Tối ưu hóa nhịp độ đóng gói thông qua các thuật toán phần mềm và giảm thời gian chờ đợi không cần thiết.
2. Cải tiến quy trình
Điều chỉnh cài đặt khối lượng chiết rót: Đặt giá trị khối lượng chiết rót hợp lý theo đặc điểm sản phẩm và nhu cầu thị trường, đồng thời cố gắng giữ khối lượng nguyên liệu trong mỗi túi đóng gói gần với giới hạn trên nhưng không vượt quá sai số cho phép, để tối đa hóa số lượng đầu ra trên một đơn vị thời gian.
Cải thiện tính lưu động của vật liệu: Đối với các vật liệu có độ lưu động kém, bạn có thể cân nhắc bổ sung thiết bị hỗ trợ dòng chảy hoặc thay đổi phương pháp cấp liệu (chẳng hạn như thêm hỗ trợ rung) để đảm bảo chúng đi vào túi đóng gói một cách trơn tru.
Rút ngắn thời gian thay khuôn: Nếu cần thay đổi thường xuyên các túi có thông số kỹ thuật khác nhau thì khuôn phải được thiết kế sao cho dễ tháo lắp và lắp đặt, đồng thời phải chuẩn bị sẵn các phụ tùng thường dùng để tạo điều kiện cho việc thay đổi nhanh chóng.
Giảm thời gian ngừng hoạt động: Thực hiện bảo trì phòng ngừa thường xuyên, phát hiện và giải quyết kịp thời các sự cố tiềm ẩn, đồng thời giảm tỷ lệ hỏng hóc, lập kế hoạch khẩn cấp hoàn chỉnh để nhanh chóng tiếp tục sản xuất nếu xảy ra sự cố;
3. Đào tạo nhân sự
Tăng cường đào tạo kỹ năng: Cung cấp đào tạo kỹ thuật đầy đủ cho người vận hành để họ làm quen với quy trình vận hành, quy trình an toàn và biện pháp khẩn cấp của thiết bị. Thành thạo các kỹ năng khác nhau giúp nâng cao hiệu quả công việc và chất lượng sản phẩm.
Thúc đẩy các hoạt động được tiêu chuẩn hóa: Xây dựng các SOP (quy trình vận hành tiêu chuẩn) chi tiết, làm rõ các yêu cầu và biện pháp phòng ngừa cụ thể cho từng bước và đảm bảo rằng tất cả nhân viên thực hiện nhiệm vụ theo tiêu chuẩn thống nhất.
Khuyến khích tinh thần đồng đội: Tạo bầu không khí làm việc tốt và thúc đẩy giao tiếp và hợp tác giữa các bộ phận khác nhau. Ví dụ: thiết lập hệ thống khen thưởng để ghi nhận những nhân viên đưa ra đề xuất cải tiến hiệu quả hoặc giúp giải quyết vấn đề.
4. Quản lý bảo trì
Thực hiện bảo trì phòng ngừa: Xây dựng kế hoạch bảo trì khoa học và hợp lý, thường xuyên kiểm tra tình trạng hoạt động của các bộ phận quan trọng như xích, bánh răng, dây đai… và thay thế kịp thời các bộ phận cũ, hư hỏng để tránh những hỏng hóc đột ngột ảnh hưởng đến sản xuất.
Duy trì sự sạch sẽ và vệ sinh: Đặc biệt đối với các ứng dụng cấp thực phẩm, phải tuân thủ nghiêm ngặt các quy định về an toàn thực phẩm, bên trong và bên ngoài thiết bị phải được vệ sinh thường xuyên để tránh tạp chất lạ xâm nhập vào sản phẩm.
Tối ưu hóa quản lý hàng tồn kho: Lập kế hoạch hợp lý việc kiểm kê các bộ phận hay bị hao mòn thường được sử dụng để đảm bảo có thể nhanh chóng có được chúng khi cần và giảm thời gian ngừng hoạt động kéo dài do thiếu phụ tùng.
Giám sát điều kiện môi trường: Duy trì nhiệt độ và độ ẩm môi trường làm việc thích hợp để tránh nhiệt độ quá cao hoặc quá thấp ảnh hưởng đến tuổi thọ của các linh kiện điện tử. Độ ẩm quá cao có thể gây ăn mòn kim loại hoặc đoản mạch điện.
5. Phân tích dữ liệu và cải tiến liên tục
Thu thập dữ liệu vận hành: Sử dụng chức năng ghi dữ liệu tích hợp của hệ thống điều khiển để thu thập thông tin về hiệu suất thiết bị, hiệu quả sản xuất, v.v. Dữ liệu này có thể giúp chúng ta hiểu rõ hơn các vấn đề trong quá trình sản xuất và tìm ra giải pháp.
Thực hiện phân tích thống kê: Phân tích dữ liệu sản xuất thông qua các công cụ như SPC (Kiểm soát quy trình thống kê) để xác định nguyên nhân gây ra biến động bất thường và thực hiện các biện pháp có mục tiêu để khắc phục chúng.
Thúc đẩy cải tiến liên tục: Dựa trên kết quả phân tích dữ liệu, liên tục tối ưu hóa quy trình sản xuất và các thông số kỹ thuật, đồng thời khám phá các phương pháp mới để nâng cao hơn nữa hiệu quả sản xuất. Khuyến khích nhân viên tham gia các hoạt động cải tiến và cùng góp phần nâng cao năng lực cạnh tranh của công ty.
Tóm lại, nâng cao hiệu quả sản xuất của máy đóng gói hạt hoàn toàn tự động là một dự án mang tính hệ thống đòi hỏi phải xem xét toàn diện từ nhiều khía cạnh như thiết bị, công nghệ, nhân sự và bảo trì. Chỉ thông qua sự đổi mới liên tục và làm việc chăm chỉ, chúng ta mới có thể bất khả chiến bại trong cuộc cạnh tranh khốc liệt trên thị trường.
Xem các sản phẩm cân đóng gói hạt:
Cân Đóng Bao Hạt Đậu Nành, Thóc, Gạo, Đỗ, Ngô, Nông Sản
Cân đóng bao cám hạt viên nén thức ăn chăn nuôi
Một số hình ảnh sản phẩm:
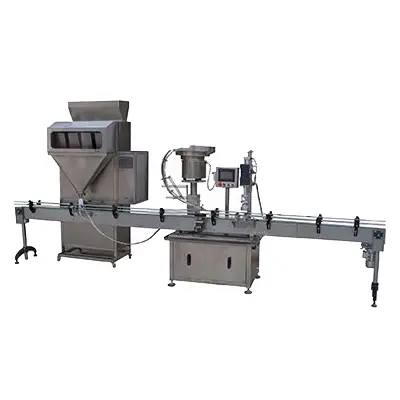
Máy đóng gói hạt tự động
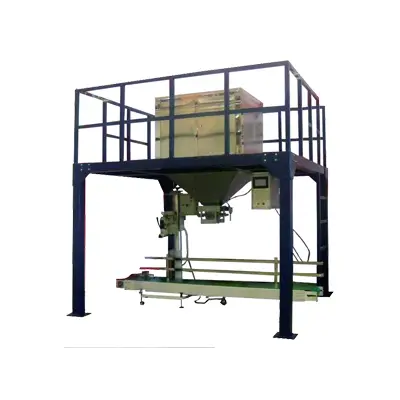
Máy đóng gói hạt tự động
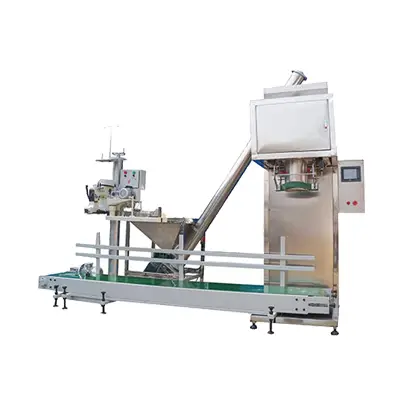
Máy đóng gói hạt tự động
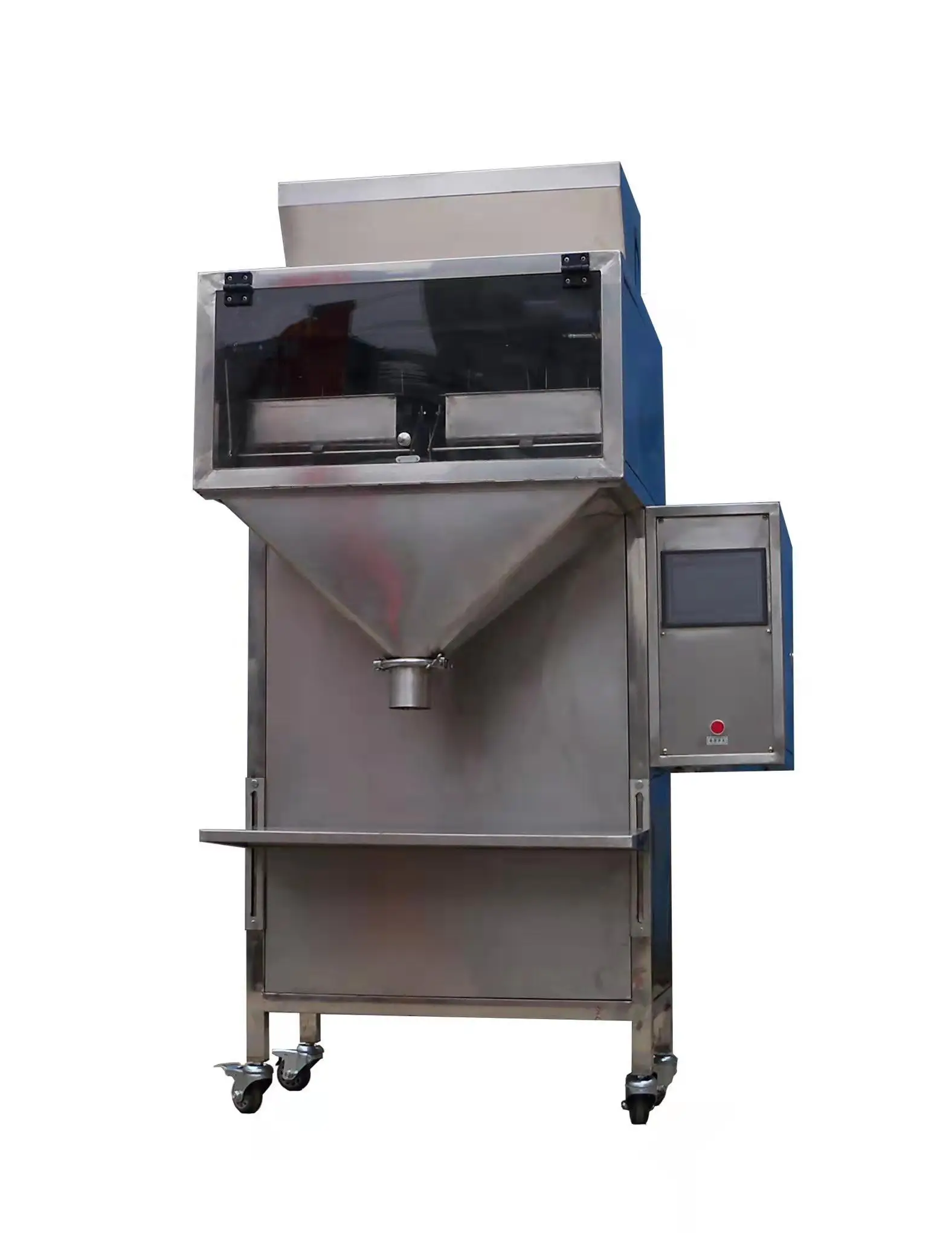
Máy đóng gói hạt tự động
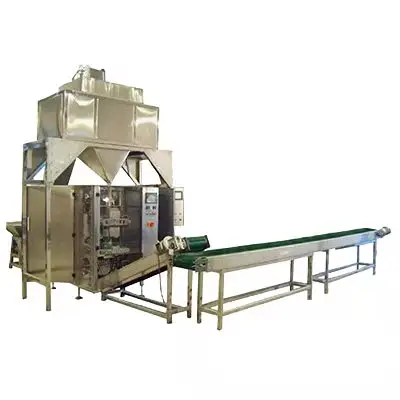
Máy đóng gói hạt tự động
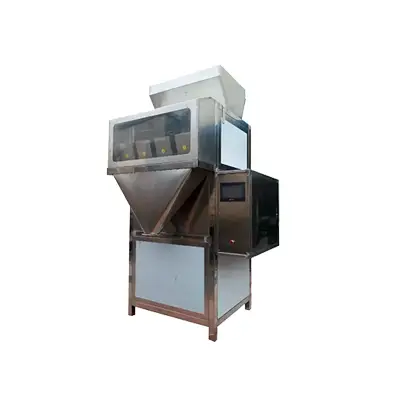
Máy đóng gói hạt tự động
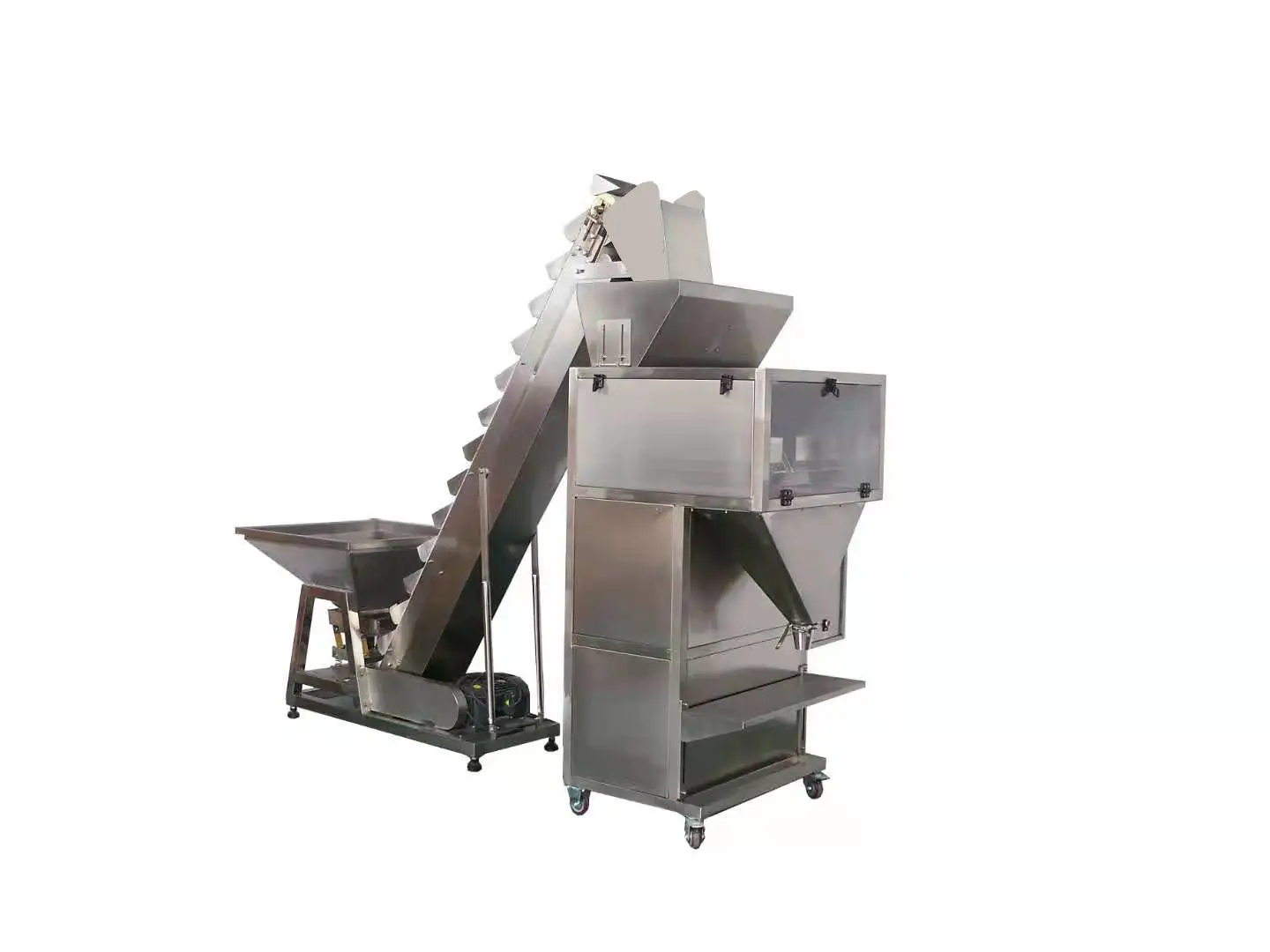
Máy đóng gói hạt tự động